Tinplate, Black Plate, TFS (Tin Free Steel) and Tin Coated Sheet
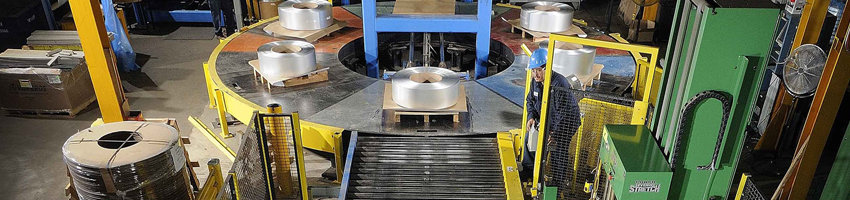
Tin mill products include electrolytic tinplate, electrolytic chromium coated steel (also referred to as tin free steel or TFS), and black plate, the uncoated steel. About 90% of tin mill products made in the world are used by the container industry in the manufacture of cans, ends, and closures for the food and beverage industry. The balance of production is used for automotive components, shelving, computer chassis, telecommunications cable, cookware, etc.
ELECTROLYTIC COATING
Electrolytic Tinplating
Black plate (basically a clean, light gauge cold rolled steel, see Steelmaking) destined for coating goes directly from either the temper mill or double cold reduction mill to the coating line. Learn about the sequence of operations that occurs in a tinplating line, at speeds up to 2000 feet per minute, below:
Electrolytic Tin Coated Sheet
Sheet and tin mill products are differentiated by gauge. Electrolytic tinplate has a maximum thickness of 135 lb. base weight or 0.0149 inch nominal thickness. Tin coated sheet starts at 0.0150 inch nominal thickness and is produced up to 0.0359 inch nominal thickness.
Use of Chromium Coating
Chromium and chromium oxide coatings, developed for food packaging in the 1960’s, offer superior lacquer adhesion and good storage properties. These coatings are mixtures of chromium metal and chromium oxides. Unlike tinplate with its multiplicity of coating weights, only a single standardized chromium-coated product is manufactured.
Electrolytic Chromium Coated Black Plate
This product, commonly referred to as tin-free steel or TFS, follows the same processing sequence as electrolytic tinplate. The coating lines are mechanically similar. During the electrolytic deposition process, chromium and chromium oxide are deposited. The metallic chromium coating on each surface is applied 5.0 milligrams (mg)/sq. ft. of area. The oxide film ranges from 0.7 to 2.0 milligrams (mg)/sq. ft., but is generally on the lower side of this range.
Unlike tin, the chromium layers cannot be reflowed, therefore a coating line dedicated to chromium coating will not have melting towers as used on the tin line to reflow the tin into a bright state.
The product is also electrostatically oiled before it exits the coating line. Historically, the industry used butyl stearate oil (BSO), which was developed for its lubricity to prevent scratching. In some instances, it has been determined that acetyl tributyl citrate (ATBC) oil used on electrolytic tinplate is more compatible with some specific lacquering and paint systems. In this case, ATBC has been preferred at the expense of the greater lubricity of the BSO.
PRODUCT CHARACTERISTICS
Tin mill products are produced with certain standardized product characteristics, including terminology, composition, mechanical properties, surface finish, coating weights, and the like. These characteristics are covered in detail in the ASTM Standard Specifications.
CLASSIFICATION OF TIN MILL PRODUCTS
The steel industry has adopted standard product names, nomenclature, and order sequencing as published by ASTM.
Black Plate
Single Reduced Black Plate (1 CR BP) – through 135 lb. base weight
Double Reduced Black Plate (2 CR BP) – through 100 lb. base weight
Electrolytic Tin Coated
Single Reduced Electrolytic Tinplate (1 CR ETP) – through 135 lb. base weight
Double Reduced Electrolytic Tinplate (2 CR ETP) – through 100 lb. base weight
Single Reduced Electrolytic Tin Coated Sheet (1 CR TCS) – starting at 0.0150 inch nominal
Electrolytic Chromium Coated
Single Reduced Electrolytic Chromium Coated Black Plate (1 CR ECCS) – through .020 inch nominal
Double Reduced Electrolytic Chromium Coated Black Plate (2 CR ECCS) – through 100 lb. base weight
Tempers
DESIGNATION | ROCKWELL HARDNESS AIM 30-T* | APPROXIMATE LONGITUDINAL YIELD STRENGTH, KSI* |
---|---|---|
T-1 BA | 49 +/- 4 | 25 – 42 |
T-2 BA | 53 +/- 4 | 34 – 46 |
T-3 BA | 57 +/- 4 | 40 – 52 |
T-4 CA | 61 +/- 4 | 48 – 60 |
T-5 CA | 65 +/- 4 | 57 – 58 |
DR-8 BA | 73 Mean | 70 – 85 |
DR-9 CA | 76 Mean | 85 – 100 |
*The values shown are the approximate range only and are not specification requirements.
Finishes
DESIGNATION | APPROX. A-A* MICROINCH RANGE | CHARACTERISTIC |
---|---|---|
5C | 30 – 60 | Standard blasted surface for black plate and some tinplate and TFS requirements. For tinplate, when the tin is unmelted, and when the 5C finish is used for black plate and TFS, the finish is often referred to as “matte” finish. On tinplate only, when the tin is melted, the finish is sometimes referred to as “silver” or “SBF”, or “brite grit”. |
7A | 5 or less | A lustrous, smooth surface typically found only on black plate intended for electroplating. It is currently not available in the U.S. |
7B | 7 – 15 | A smooth finish that may contain fine grit lines. Usually used only for tinplate that is melted after plating and then it’s often referred to as “bright” finish because the surface is very smooth and reflective. Limited availability, only made by a few mills. |
7C | 12 – 22 | A smooth finish with grit lines. This is the most common finish for tin mill products, especially tinplate and TFS though black plate can be ordered with this finish. When used for tinplate that is melted after plating, or for black plate or TFS, the finish is commonly referred to as “stone” finish |
Base Weights
BASE WEIGHT | THICKNESS (IN/MM) |
---|---|
53 | 0.0058 / 0.15 |
55 | 0.0061 / 0.155 |
57 | 0.0063 / 0.16 |
60 | 0.0066 / 0.17 |
63 | 0.0069 / 0.175 |
65 | 0.0072 / 0.18 |
68 | 0.0075 / 0.19 |
70 | 0.0077 / 0.195 |
73 | 0.0080 / 0.20 |
75 | 0.0083 / 0.21 |
78 | 0.0086 / 0.22 |
80 | 0.0088 / 0.22 |
83 | 0.0091 / 0.23 |
85 | 0.0094 / 0.24 |
90 | 0.0099 / 0.25 |
93 | 0.0102 / 0.26 |
95 | 0.0105 / 0.27 |
98 | 0.0108 / 0.275 |
100 | 0.0110 / 0.28 |
103 | 0.0113 / 0.29 |
105 | 0.0116 / 0.295 |
107 | 0.0118 / 0.30 |
112 | 0.0123 / 0.31 |
115 | 0.0127 / 0.32 |
118 | 0.0130 / 0.33 |
123 | 0.0135 / 0.34 |
128 | 0.0141 / 0.36 |
135 | 0.0149 / 0.38 |
Tin Coatings - Standard Coating Weights
COATING WEIGHT DESIGNATION (US) [EURO] | NOMINAL TIN COATING WEIGHT EACH SURFACE, LB./BASE BOX (US) [EURO] |
---|---|
(05) [0.55/0.55] | (0.025/0.025) [0.55/0.55] |
(10) [1.1/1.1] | (0.05/0.05) [1.1/1.1] |
(20/05) [2.2/0.55] | (0.10/0.025) [2.2/0.55] |
(15) [1.7/1.7] | (0.075/0.075) [1.7/1.7] |
(20/10) [2.2/1.1] | (0.10/0.05) [2.2/1.1] |
(20) [2.2/2.2] | (0.10/0.10) [2.2/2.2] |
(25/20) [2.8/2.2] | (0.125/0.10) [2.8/2.2] |
(25) [2.8/2.8] | (0.125/0.125) [2.8/2.8] |
(50/20) [5.6/2.2] | (0.25/0.10) [5.6/2.2] |
(50/25) [5.6/2.8] | (0.25/0.125) [5.6/2.8] |
(75/20) [8.4/2.2] | (0.375/0.10) [8.4/2.2] |
(50) [5.6/5.6] | (0.25/0.25) [5.6/5.6] |
(75) [8.4/8.4] | (0.375/0.375) [8.4/8.4] |
(100) [11.2/11.2] | (0.50/0.50) [11.2/11.2] |
(75/25) [8.4/2.8] | (0.375/0.125) [8.4/2.8] |
(100/20) [11.2/2.2] | (0.50/0.10) [11.2/2.2] |
(100/25) [11.2/2.8] | (0.50/0.125) [11.2/2.8] |
One pound of tin per base box (shared over both surfaces) is equivalent to approximately 0.000060 inch thickness on each surface. This list represents standard coating weights. Others available upon inquiry.